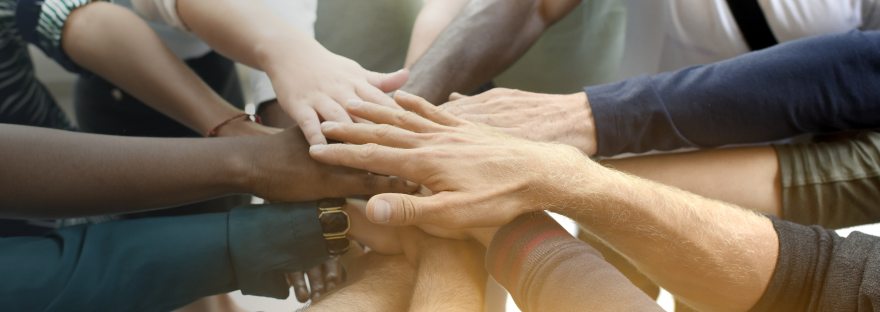
For many people who work outside of construction, it might not occur to them that the industry has impacts that reach much further than the building of roads, skyscrapers and homes.
In fact, by embracing new technology and new ways of viewing the world, the construction industry is in a position to set the standard for others to follow, when it comes to the use of technology, and its impact on economics, other industries and the environment.
The World Economic Forum issued a report called “Shaping the Future of Construction: A Breakthrough in Mindset and Technology” that said, among other things:
“The world is changing faster than ever before. Consider just one of the global megatrends shaking up the construction industry: the population of the world’s urban areas is increasing by 200,000 people per day, all of whom need affordable housing as well as social, transportation and utility infrastructure. In the face of such challenges, the industry is almost under a moral obligation to transform.
Its transformation will have transformative effects elsewhere: on the wider society, by reducing construction costs; on the environment, by improving the use of scarce materials or by making buildings more eco-efficient over time; and on the economy, by narrowing the global infrastructure gap and boosting economic development in general.”
Three areas of innovation stand out in terms of their maximum impact to the industry, and the world around us:
Automation
There is a lot to be gained from automation on the construction site, not the least of which is productivity. Using automation and robotics to engage in repetitive or remote tasks has advantages that are measurable against the bottom line of a project:
- Machine monitoring can prevent rework and downtime costs due to error or machine failure.
- Accuracy and precision of a task is improved.
- Safety is improved by increasing overall monitoring, local and remote, to ensure that everything is being completed according to approved specifications or within tolerance limits.
“Komatsu, a Japanese manufacturer of construction equipment, is developing automated bulldozers incorporating various digital systems. Drones, 3D scanners and stereo cameras gather terrain data, which is then transmitted to the bulldozers; these are equipped with intelligent machine-control systems that enable them to carry out their work autonomously and thereby speed up the pre-foundation work on construction sites, while human operators monitor the process. On mining sites, autonomous haul trucks are already in common use.” (Source)
3D Printing
One of the major costs in construction is the raw materials used. By leveraging technology like 3D printing, even if only for components, major cost savings are available to companies of all sizes. Speed, accuracy, and less waste are all functions of being able to create materials on a needs basis.
“The technology enables the production of purpose-built shapes that cannot be produced by any other method; it promises productivity gains of up to 80% for some applications, together with an important reduction in waste. Construction time for some buildings could shrink from weeks to hours, and customized components could be provided at much lower cost.” (Source)
The ability to create and leverage newer forms of materials can affect the economics of a project, the quality of the final result, and the environmental impact as well. The construction industry worldwide is the largest consumer of raw materials and resources (renewable and non-renewable). By engaging and indeed encouraging the production of higher quality materials, based on new technologies like 3D printing, even small changes can make a big difference.
Why? The US construction industry produces a total of 40% of the solid waste for the entire country.
“Throughout the world, such waste involves a significant loss of valuable minerals, metals and organic materials – so there is great opportunity to create closed material loops in a circular economy…
Increasingly, sustainability is becoming a requirement rather than just a desirable characteristic, and its pursuit is bound to affect both the construction process and the built asset itself. The construction sector produces an enormous amount of waste, so the more efficient use and recycling of raw materials, even a small improvement, offer huge potential benefits. ” (Source)
Big data and digitalization of the worksite
Above, we mentioned that machine monitoring as a part of automation can have a major impact to productivity but digitalization of projects can go so much further both in terms of productivity and cost savings. That’s because it can be leveraged throughout the construction cycle, from early design, preventing issues that might otherwise slow down productivity, create waste through errors and so on. Scope, time and costs can all be monitored at a granular level, ensuring that budgets and schedules are adhered to without compromising quality or safety.
“New methods of simulation and virtual reality help to identify interdependencies and clashes (clash detection) during the design and engineering stages, and enable a virtual experience of the building even in the early design phase. By exploiting mobile connectivity and augmented reality, companies can engage in real-time communication and provide workers with additional on-site information.” (Source)
“According to a recent study, full-scale digitalization in nonresidential construction would, within 10 years, be capable of producing annual global cost savings of $0.7-1.2 trillion (13-21%)“ (Source)
All planned aspects of a project, from general management to figuring out human resources required, as well as materials, suppliers and subcontractors, can all be sped up and developed more accurately with digitalization and the use of real time data. Even from project to project, best practices and standards can be shared and leveraged, to save time and resources.
What stands in the way of this change of mindset?
While change can inspire fear, it can also be the foundation to champion future generations to grow in an industry that is without limits and will always have huge impacts on the economy, locally and around the world. The construction industry affects so many others—it is considered a horizontal industry, for that very reason!
“To mention a few, residential housing accounts for 38% of global construction volume; transport, energy and water infrastructure 32%; institutional buildings 6%; commercial buildings 12%; and industrial sites (from cement to automotive manufacturing) 13%. For all of these sectors, value creation almost always occurs within or by means of buildings or other constructed assets.” (Source)
Finding ways to get past the bias that might favor traditional methods is the step forward that we all need to take to keep moving forward as a vital industry in the United States and beyond.
About the author
Terri Olson is an investor and Vice President with OE Construction Corp., a commercial excavation and underground utility contractor. She has worked in the construction industry for over 13 years and brings over 25 years of experience in building and running technology companies. Running a construction company is a lot like a tech company, nothing is ever the same, every day is a new adventure. Her son, Chris Olson, is the founder of OE Construction Corp. and started working in the construction industry in high school. He founded the company at 19 years old and his passion for the people, the equipment, the work and the challenge to excel has kept him going. Chris has brought in new technology over the years and we are now 100% machine control when building large sites and his expertise in working with GPS and drones has taken us to the next level in earthwork, pretty cutting edge and exciting.