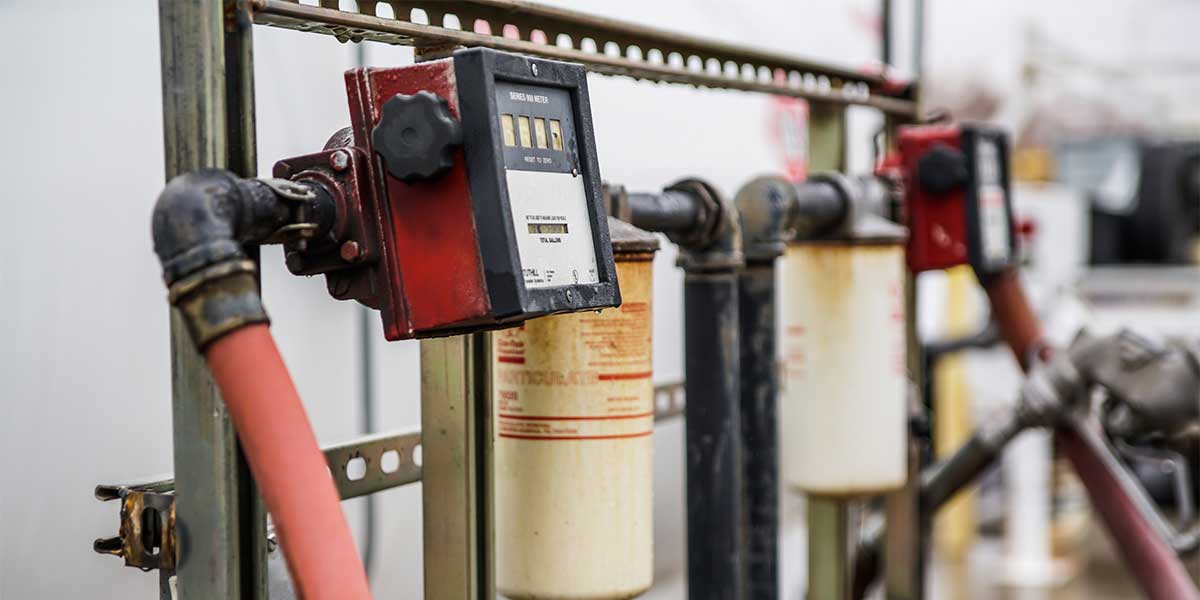
Most of us expect our cars to provide alerts for tune-ups, oil changes, or filter replacements. Keeping cars running smoothly is easy when we are reminded of when to perform maintenance. Condition-based maintenance (CBM) in the construction industry follows the same principle, yet not everyone in the equipment sector takes full advantage of this time- and cost-effective system.
CBM is a no-brainer for construction equipment. A machine idling on a job site for 250 hours using 200 gallons of fuel has less internal wear than one working at full capacity for the same amount of time. So why do we base our preventative maintenance schedules on hours, miles, and days?
Our use of the “oil life percentage” systems in our personal vehicles shows that we trust alerts to keep our cars running. Perhaps the lack of confidence in OEM technology and telematics’ ability to accurately report machine fuel burn is why some fleet managers still don’t totally depend on CBM.
Telematics can provide reliable fuel burn data in a timely manner to reduce oil-drain intervals. In addition to fuel burn data, OEM engine-control modules have many more data points to inform equipment managers on their units’ performance. Through telematics, machines can transmit accurate fuel use data directly to an end-user’s maintenance program. Although telematics’ fuel use data is currently delivered as a running total in the AEMP telematics standard, a simple math formula can calculate hourly fuel burn. Many maintenance software programmers are addressing the future benefits of CBM when partnered with scheduled oil-sampling programs. They are expanding their formulas and preventative maintenance triggers to include fuel burn, a long-sought after benchmark.
With all the new emission after-treatments, exhaust filters, and emission systems, what is the correct fuel burn target for optimum oil-drain intervals? 15 years ago, the Caterpillar bulletin #SEBD0794 calculated 70 gallons of fuel burned per quart of oil for a premium quality HD diesel engine oil. Exhaust particulates and soot that engines used to expel through the exhaust have to be captured (possibly in the oil) or burned elsewhere. These changes in the engine exhaust emissions reinforce the need for CBM to be partnered with a scheduled oil sampling (SOS) program. Recent advancements in machine technology have reinforced the importance of data produced by SOS programs.
Current information technology and telematics present major challenges to OEMs and lubricant providers. Working with both parties, we will need to determine data such as fuel burn baseline ratios to bring faith in CBM to the masses.
The focus needs to be on when the maintenance needs to happen, not what needs to be maintained. The best way to do this is by using reliable and timely fuel burn data reinforced with a scheduled oil sampling program – in essence, a condition-based maintenance system.
About the author
Daniel Samford CEM, principal of Peak Performance Asset Services LLC, consults in fleet management, mixed fleet telematics integration, negotiations for specialized construction equipment and annual vehicle purchases, national accounts, and fleet value evaluations. Previously with Herzog Companies for 21 years, Samford managed a fleet of over 2,800 units and 700 vehicles with a replacement cost of over 250 million dollars in operations throughout the continental U.S., Alaska, Canada, Mexico, Guam, and the Caribbean. He has been directly involved in equipment ownership and operating evaluations throughout his career. Samford sits on the AEMP Board of Directors, its Telematics Futures committee, and has been vocal on the need for a unified telematics language and single portal equipment management for the construction equipment industry. He can be contacted through his website www.PPASllc.com or at dsamford@PPASllc.com
Have an article that you would like to contribute? Click here to contact us.